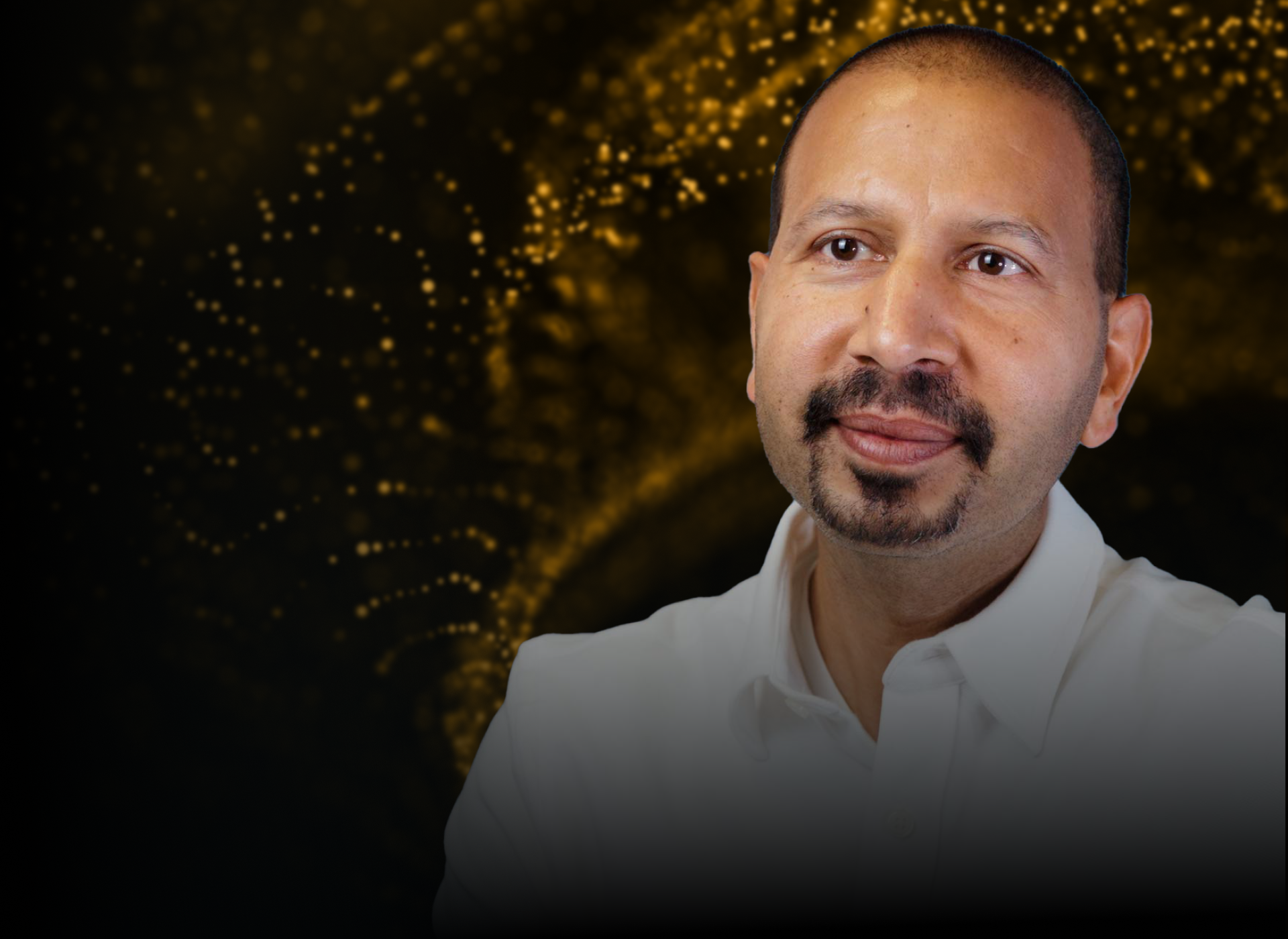
Suvi Sharma
CEO
SOLARCYCLE
Return to the magazine
Solar, Full Circle
SOLARCYCLE is turning end-of-life panels into a renewable resource—reclaiming materials and reshaping the solar supply chain.
Although it’s a relatively new industry, solar dominates 80% of new power-generating capacity in the United States. More than one billion solar panels are manufactured each year globally—and that number is projected to triple within eight years. But “mind-boggling” growth comes with challenges, says Suvi Sharma, CEO of SOLARCYCLE, which provides an eco-friendly process for decommissioning solar panels and repurposing the materials. In the United States alone, millions of panels are reaching end of life every year, and Sharma expects that total to surge to tens of millions by 2030. “All good things come to an end, and so do solar panels,” he says.
SOLARCYCLE’s proprietary, patented technology enables the company to extract 95% of the value of a solar panel’s materials, including silver, silicon, copper and aluminum. All are worth their weight in gold, given that new solar panels consume nearly 20% of the world’s annual supply of silver—and making new aluminum products from recycled frames requires 95% less energy than mining bauxite.
That said, recycling has two fundamental challenges. The first is logistics, because solar is everywhere: on homes, on commercial rooftops and in utility-scale solar farms. “There’s a lot to collect,” says Sharma. Then there’s the issue of taking apart intentionally resilient products. “Solar panels are really robust,” he explains. “They’ll last for 20 years in outdoor conditions, which means they’re a really strong product and don’t come apart easily.”
SOLARCYCLE combines mechanical and thermal processes to extract materials, but the company increasingly favors thermal because it allows for cleaner separation. Sharma likens the panels to a sandwich whose ingredients are glued together, requiring heat to separate them efficiently. “If you just crush and shred everything, you’ll get a mishmash of junk,” he says.
SOLARCYCLE has also begun to address the final frontier of solar recycling: plastic components that make up the 5% of materials the company is unable to reclaim. Its R&D team is developing solutions to transform plastics into packaging for SOLARCYCLE’s own operations—the pallets and protective material needed for transportation.